STi FR3AK
Armyssoldierboy
Have a rough idle but runs fine through the gears then dies when you press in the clutch or stop? It's probably a vacuum leak. In here I will discuss how to build a tester for ~$20 provided you already have or have access to an air compressor. If not, it's a good investment as well and I got a really good one for $200. Anyways,
Tools needed:
Flathead screwdriver
Phillips screwdriver
Tube of silicone
Drill was helpful but not needed
Gloves and eyepro
air compressor
or
bike pump (though it's not as effecient)
**Ok, when you do this, you need to do the test post-maf so you don't run the risk of ruining the maf sensor (so I've heard) plus it keeps you in the engine bay if you're running a cold air intake.**
1. First take off the maf sensor (BLUE ARROW). You can either unclip it then unscrew it with your phillips head or just unscrew it and safely lay it aside somewhere.
2. Whatever intake you're using, you need to take it off by undoing the clamp to the turbo inlet (RED ARROW) using a flathead screwdriver.
3. Undo the last clamp on the coupler (YELLOW ARROW) as this is what you really need.
4. Now that you have your intake coupler, head over to your local Home Depot, Lowes or whatever, it's time to assemble your tester.
5. Once there, take your coupler to the pvc piping section and try to find:
-a PVC female adapter socket
-a male screw in cap that will fit inside your turbo inlet coupler like this

-a male industrial fitting for the air compressor.
or
-a valve stem for the bike pump
Tools needed:
Flathead screwdriver
Phillips screwdriver
Tube of silicone
Drill was helpful but not needed
Gloves and eyepro
air compressor
or
bike pump (though it's not as effecient)
**Ok, when you do this, you need to do the test post-maf so you don't run the risk of ruining the maf sensor (so I've heard) plus it keeps you in the engine bay if you're running a cold air intake.**
STEPS 1-3 refer to this pic
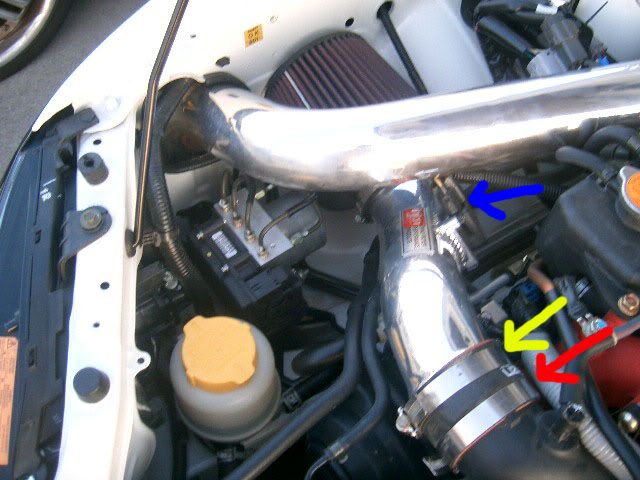
1. First take off the maf sensor (BLUE ARROW). You can either unclip it then unscrew it with your phillips head or just unscrew it and safely lay it aside somewhere.
2. Whatever intake you're using, you need to take it off by undoing the clamp to the turbo inlet (RED ARROW) using a flathead screwdriver.
3. Undo the last clamp on the coupler (YELLOW ARROW) as this is what you really need.
4. Now that you have your intake coupler, head over to your local Home Depot, Lowes or whatever, it's time to assemble your tester.
5. Once there, take your coupler to the pvc piping section and try to find:
-a PVC female adapter socket
-a male screw in cap that will fit inside your turbo inlet coupler like this

-a male industrial fitting for the air compressor.
or
-a valve stem for the bike pump
6. Now you might have to use some enginuity (I even asked for help since I couldn't find the exact size I needed) in finding the pieces. This is what mine came out like:
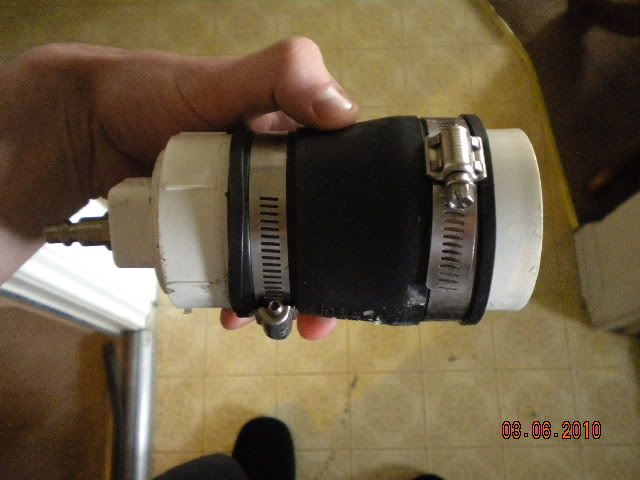
Not the prettiest thing but it works. I had to use a coupler that I stretched to fit one end and clamped the *%&* out of the other end.
7. Ok so now you have all your pieces. Take the silicone and squirt some on the threads to the PVC cap threads and spread it over all the threads for the best seal. Screw it into the female socket. Let it dry for an hour or so to be sure it's dry.
8. Now you need to make a hole on the top square piece of the PVC cap for the air fitting. A drill made it super easy. DON'T MAKE IT TOO BIG. Take the industrial fitting and attempt to screw it into the cap. It will self tap if you can get it started, which you want. If you do make the hole too big, I'm sure you can use washers etc but you just made it more time comsuming.
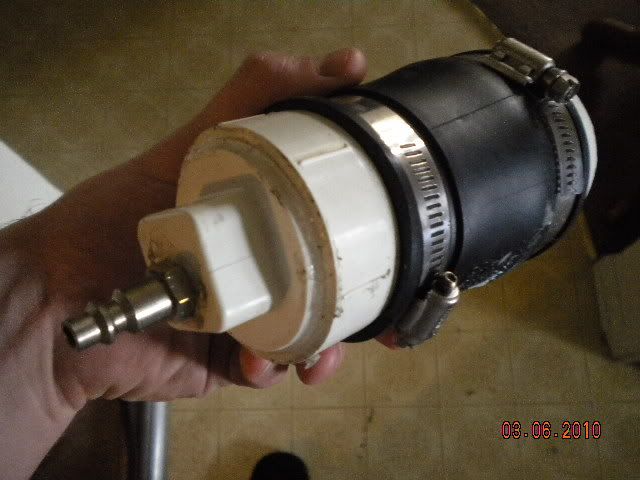
9. After you got your fitting in there nice and snugg, get that silicone again and I went ape poop in the underside of the cap to ensure there were NO leaks around the fitting, threads of the cap etc. Be sure not to cover the fittings air exit (duh). Let all that dry. Check it every so ofter after about 30-45min. If it's not completely dry and you run air through it, it's just going to blow through the silicone and leak.
10. Now get the clamps to secure this to the turbo inlet coupler and back to the inlet.
*Wear your glasses/goggles for this part*
11. Hook up your air compressor or bike pump to the fitting and run 20psi through the system. If you're running 25psi on your setup, if something is going to leak or come loose, 20psi is enough. If something pops off with 20psi, it can cause injury!
11. Hook up your air compressor or bike pump to the fitting and run 20psi through the system. If you're running 25psi on your setup, if something is going to leak or come loose, 20psi is enough. If something pops off with 20psi, it can cause injury!
12. Look, listen and feel for leaks around:
-the turbo inlet @ the turbo
-turbo inlet fittings to the intake manifold
-pcv lines which are behind the stock fpr. It's between the turbo inlet/ turb and throttle body, directly behind the manifold, coming from the block.
-throttle body vacuum lines such as the blue areas shown here:
-the turbo inlet @ the turbo
-turbo inlet fittings to the intake manifold
-pcv lines which are behind the stock fpr. It's between the turbo inlet/ turb and throttle body, directly behind the manifold, coming from the block.
-throttle body vacuum lines such as the blue areas shown here:
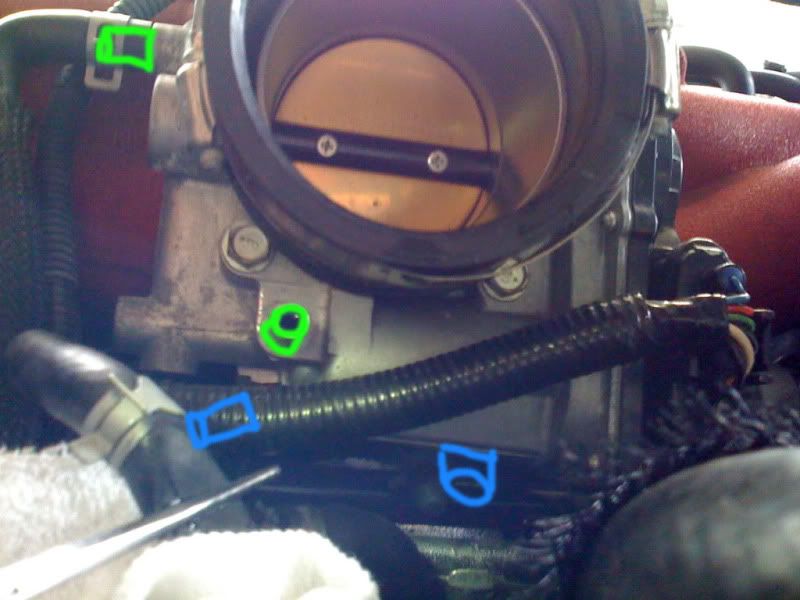
Those are just SOME examples. If it's a small leak, you'll hear a hiss, look for small lines. If it's a huge one, you'll feel it but might not hear it. Take off your gloves and feel for cool air and stick your head close to the lines (with your eyepro on). Hope you guys find your leaks I found 4 :tard:
Last edited: